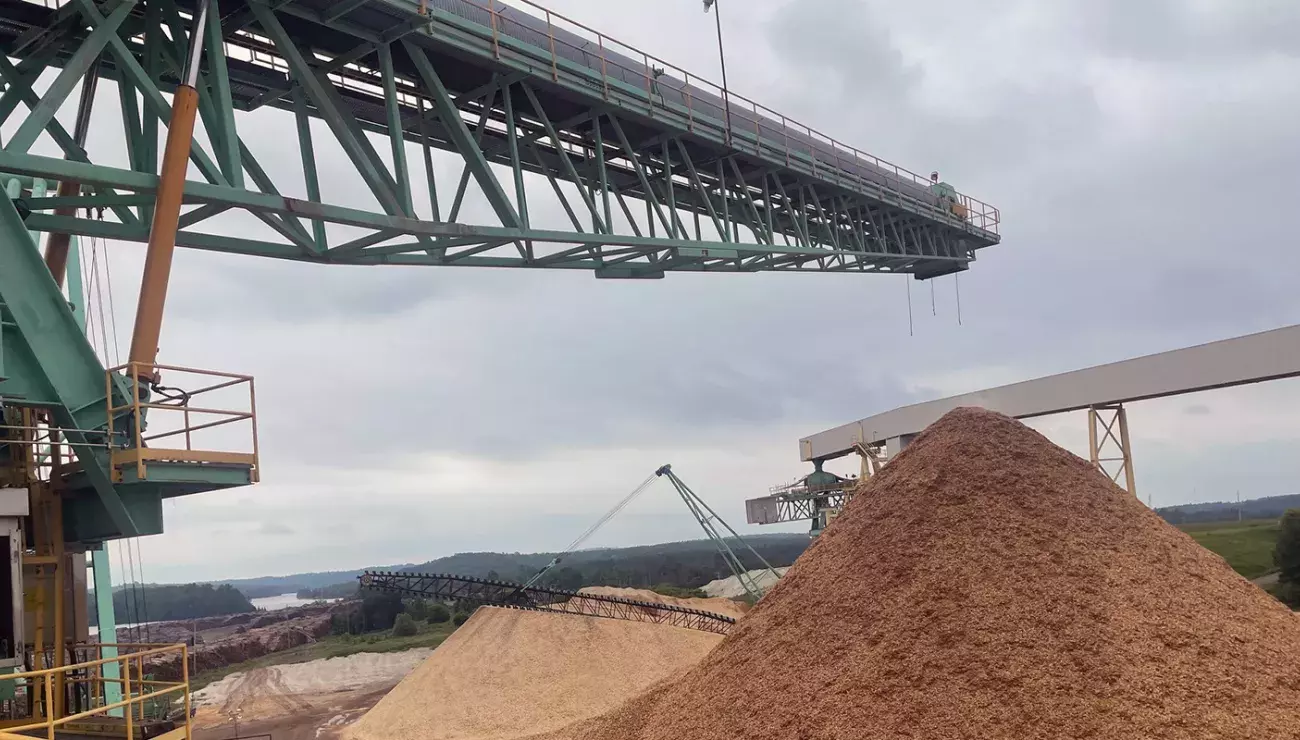
24 years of service and still going strong
20 Sep 2021With winter temperatures dropping down to more than minus 20 degrees Celsius, Domtar’s Espanola paper mill, located on the banks of the Spanish River in Northern Ontario, Canada, knows what it takes to successfully operate all-year-round, whatever the weather.
Established in the early 1900s by the Spanish River Pulp & Paper Company, and acquired by Domtar in 1998, the mill produces 69,000 tons of over 200 different grades of technical and specialty paper every year, including northern bleached softwood kraft pulp. It has also grown to support some 450 jobs, making the mill the largest employer in Espanola.
At its heart is a 280,000-ton annual capacity fiber line, which is fed a mix of aspen, maple and birch hardwood chips, and meeting this appetite for more than 24 years, are cold weather stacker reclaimers from Bruks Siwertell.
Since their installation in 1997, the two fully automated circular systems, with a beam length of 41.5m, have made light work of the requirements from this massive woodyard, operating almost continuously, even in the harshest winters, with minimal operator intervention and downtime.
Taking the heat out
Espanola’s Bruks stacker reclaimers take delivery of new wood chips and organize and arrange them into even piles. Their automated processes produce controlled layers of materials, which are effectively blended as the wood chips are reclaimed. This blending process smooths spikes in material variability; important when sources that feed the piles are different in some way, such as size distribution or moisture content. Automated systems handle these variations with ease; manual pile management keeps these different materials together on the pile so they are reclaimed sequentially.
Blending is also particularly vital for organic commodities such as wood chips, bark and sawdust. It protects the integrity of the chips by reducing fiber losses from microbial action and heat build-up in the pile, maximizing safety and helping operators, such as Domtar, to ensure the highest quality end-product.
Repeatable, impressive performance
Although they have an impressive service record, Espanola’s stacker reclaimers are not unique in this capability. In fact, their twins, two further Bruks circular cold weather stacker reclaimers operate for Domtar’s Dryden paper mill, also in Ontario. These systems have been delivering similar outstanding operational advantages for an equally long length of time.
“The ability of our automated woodyards to deliver consistently high reliability and performance, even in these extreme climates, for many, many years, is a huge advantage,” says Joanne Turnell, Sales Representative, Canada, Bruks Siwertell. “Domtar benefits from this, and supports its operations with a strong, skilled, independent maintenance crew that carries out regular service work, keeping its machines in good condition. Except for assistance with a center pivot bearing two years ago, Domtar’s machines have required very little input from us over the years.”
Piling up savings
Automated woodyards bring other key operational advantages. “The biggest benefit of any automated stacking and reclaiming system is cost saving,” continues Turnell. “Bruks cold weather stacker reclaimers are extremely efficient, even in snow and ice conditions, and require no operator or attendant. When you compare this to using and maintaining expensive operator-driven, mobile equipment, 24-hours-a-day, with its associated fuel consumption demand, it is clear to see where the savings start to add up.
“Removing mobile equipment from the woodyard has other benefits as well,” she adds. “Wheeled loaders can damage wood chips and other sensitive materials as they drive over the pile. Our stacker reclaimers eliminate this issue.
“Furthermore, the carbon footprint of an electricity-driven stacker reclaimer is a fraction of a diesel-driven, loader-managed pile,” explains Turnell. “Adding to their environmental credentials, they have completely covered conveyors. This eliminates dust and spillage along the conveying lines, which reduces emissions and housekeeping issues.”
Sustainable paper production
As a company, Domtar is the largest producer of freesheet paper in North America. Since 2010, Domtar has reduced greenhouse gas emissions from its twelve paper and pulp mills by around a third and now uses around 75 percent of renewable electricity to power them. Like other Domtar mills, Espanola has gained a number of sustainability achievements.
Domtar’s Espanola mill comes highly recommended by the forestry industry, with certification by the Forestry Stewardship Council, the Sustainable Forestry Initiative, and the Programme for the Endorsement of Forestry Certification.
Finding optimal solutions
Bruks Siwertell offers one of the most comprehensive stacker reclaimer portfolios on the market, and in addition to wood products, can handle a wide range of materials from aggregates, coal and iron ore to grains, and sulfur. Depending on the application and dry bulk material handled, the shaped of the pile will deliver different advantages. Bruks Siwertell’s stacker reclaiming systems can form linear, semi-circular and fully circular piles in a range of sizes and capacities.
“Our systems are genuinely customer-driven, we work closely with our customers to develop engineered solutions exactly tailored to meet the needs of stockyards and storage facilities, taking into consideration the material being stored and the density and angle of repose and location. This ensures that the combination of technology selected works seamlessly together.
“All our stacker reclaiming systems are automated, delivering the highest possible operational efficiency for the lowest possible lifecycle costs. We talk a lot about how automation will change industries, and this is undeniably true. However, some industries have been able to benefit from these advances for much longer than people might expect, and Domtar’s Espanola and Dryden mills are just two of them,” concludes Turnell.
For more information, please send an email to sales.atlanta@bruks-siwertell.com